teamzr1
Supporting vendor
I was driving my 1993 Cadillac Sedan Deville 60 Special 1 week ago
I have owned it for 23 years and has over 273,000 miles on it
This is front week drive, engine L26 which is a 4.9L engine that fricking sits sideways, so the front of the engine is about 2 inches away
from the right front frame rail :-(
So driving it and then out of the blue barely steer this 2 ton tank, I thought a front tire went down
I had just bought food, some frozen and did not want to get stuck and have it all melt, so I tanked this for 3 miles home
Reminded me back in the 1960s when I had a 1954 Buick Roadmaster with a big block and had no power steering
Popped the hood to find the serpentine belt popped off so had no power steering alt, cooling pump or A/C
Fought getting the belt back on, started engine and belt popped off again, crap
Bought a new belt, fought getting that on and same results, had to order a new belt tensioner and when getting it and installed with new belt
Started engine and in 30 seconds hear 2 loud clunks
Find the shaft for the coolant pump snapped, so now the pulley is broken off but cannot get it out as the frame rail is only like 2 inches from pulley
and with the shaft still on the pulley, there is zero room to pull the pulley outward to get it and shaft out !
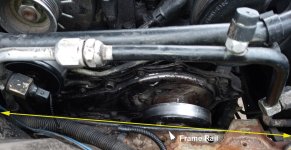
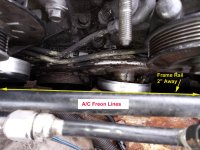
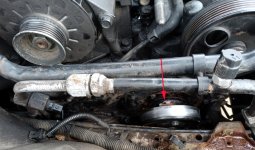
To make it worse, even though the pump itself is only 3 1/2 inches diameter it is part of the whole front cover and there are 19 bolts for that cover all
hidden and 4 of them are behind the pulley so cannot get the cover off !
New one , see the mounting plate and shaft
I cannot get the 3 bolts off the old one as broken off, no way to hold pulley to not move while trying to break loose the 3 bolts
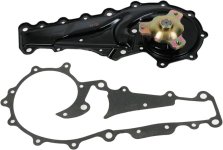
So issue is what sneaky way you think can get to snap the steel shaft housing off the cover to get the pulley and mount off so I can than fight getting cover off ?
No, I cannot raise or lower engine with car sitting outside or torch off the shaft ?
New pumps do not come with a pulley and finding one of a car 32 years old, so I do not want to damage the existing one
OK, guys come up with a sneaky way to get the shaft housing, that also has a steel bearing case busted off !
Thanks
I have owned it for 23 years and has over 273,000 miles on it
This is front week drive, engine L26 which is a 4.9L engine that fricking sits sideways, so the front of the engine is about 2 inches away
from the right front frame rail :-(
So driving it and then out of the blue barely steer this 2 ton tank, I thought a front tire went down
I had just bought food, some frozen and did not want to get stuck and have it all melt, so I tanked this for 3 miles home
Reminded me back in the 1960s when I had a 1954 Buick Roadmaster with a big block and had no power steering
Popped the hood to find the serpentine belt popped off so had no power steering alt, cooling pump or A/C
Fought getting the belt back on, started engine and belt popped off again, crap
Bought a new belt, fought getting that on and same results, had to order a new belt tensioner and when getting it and installed with new belt
Started engine and in 30 seconds hear 2 loud clunks
Find the shaft for the coolant pump snapped, so now the pulley is broken off but cannot get it out as the frame rail is only like 2 inches from pulley
and with the shaft still on the pulley, there is zero room to pull the pulley outward to get it and shaft out !
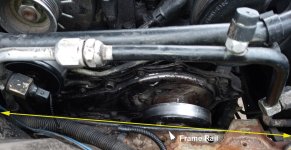
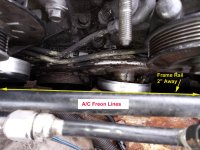
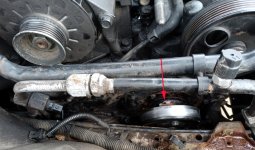
To make it worse, even though the pump itself is only 3 1/2 inches diameter it is part of the whole front cover and there are 19 bolts for that cover all
hidden and 4 of them are behind the pulley so cannot get the cover off !
New one , see the mounting plate and shaft
I cannot get the 3 bolts off the old one as broken off, no way to hold pulley to not move while trying to break loose the 3 bolts
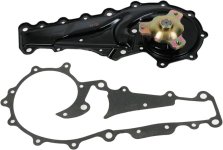
So issue is what sneaky way you think can get to snap the steel shaft housing off the cover to get the pulley and mount off so I can than fight getting cover off ?
No, I cannot raise or lower engine with car sitting outside or torch off the shaft ?
New pumps do not come with a pulley and finding one of a car 32 years old, so I do not want to damage the existing one
OK, guys come up with a sneaky way to get the shaft housing, that also has a steel bearing case busted off !
Thanks