In my last post I think I mentioned that I had had a problem that required me to do some rework.
I had managed to get to this point (see pic) where I had welded in the passenger side hinge post in place and was attempting to fix the lower windscreen surround. As you might expect before fully welding it to the sill I had checked as many dimensions as possible to ensure that it was in the right place. Or so I thought ....
However, no matter how hard I tried, when I fitted the lower windscreen support that goes across the car, I could not get the distance from the top of the windscreen to the bottom to be the same on both sides - it was about 10mm out, so not even close. Much head scratching later, and I mean hours and hours of checking and rechecking dimensions, I still could not see why this should be. I also couldn't see why only one dimension was out - surely there should be another one which is wrong by the same amount in the opposite direction? Everything else matched.
Christmas intervened and after a short break of cold weather and warm festivities I relooked at the problem with fresh eyes and decided to measure a few things that I hadn't tried before. The first breakthrough came when I measured the angle that the windscreen has with the rest of the car on each side. Making up a quick comparison tool with two straight edges, a clamp and a spirit level I realised that the side windscreen supports were at a slightly different angle to each other. This lead to the discovery that the hinge post was also very slightly off the vertical leaning backwards.
Unfortunately the only resolution was to take off the hinge post, readjust the angle between the hinge post and the screen surround (the top of the windscreen surround was perfectly in position - the lower end had slipped out of its spot at some point ) and then reattach (top and bottom of the hinge post). The hinge post was carefully removed sacrificing the attachment brace at the bottom in order to preserve the post itself.
A new one hinge post lower brace was fabricated - I had kept the template - and refitted... Here checking the fit prior to assembly.
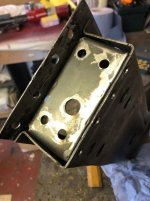
Hinge post sitting nicely....
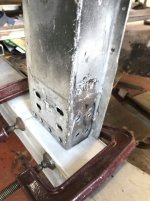
And with boot.. To be welded on when I am absolutely sure that everything else on the bird cage is finished.
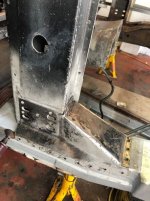
With hinge post clamped in place the lower surround was refitted. This time everything fitted perfectly with precise measurements left and right, top and bottom. You live and learn
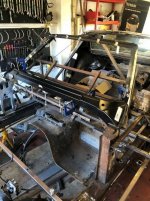
Here's a shot post welding with the firewall in place. The hinge post is now welded in position and the main pieces of the lower surround are rivetted together to keep them locked in position, prior to final fit.
A few things left to do but the next thing on the list is to tidy this up a bit...
TTFN.