teamzr1
Supporting vendor
Hi Clive F
In most cases do not need to get the PCB (circuit board) removed from the case
If having to do that you have to dig out the sealer that is like a glue and then yank PCB off mounts
Most times the failure is the relay overheating, bad contacts and gets hot enough to cause the solder joints to break
I do is dig the crap out around relay, desolder the legs and pull relay out from the underside of PCB.
New relay I cut the legs shorter and then from underside line legs up through PCB and then solder legs
I also resolder other joints
This is more of a pain in ass to do but can be done without taking PCB off and the relay only costs like $2 (USA)
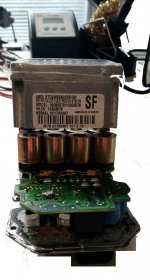
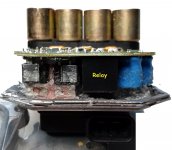
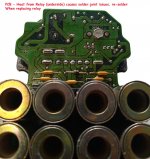
In most cases do not need to get the PCB (circuit board) removed from the case
If having to do that you have to dig out the sealer that is like a glue and then yank PCB off mounts
Most times the failure is the relay overheating, bad contacts and gets hot enough to cause the solder joints to break
I do is dig the crap out around relay, desolder the legs and pull relay out from the underside of PCB.
New relay I cut the legs shorter and then from underside line legs up through PCB and then solder legs
I also resolder other joints
This is more of a pain in ass to do but can be done without taking PCB off and the relay only costs like $2 (USA)
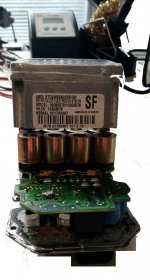
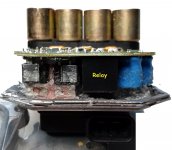
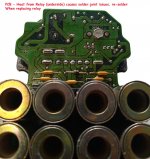